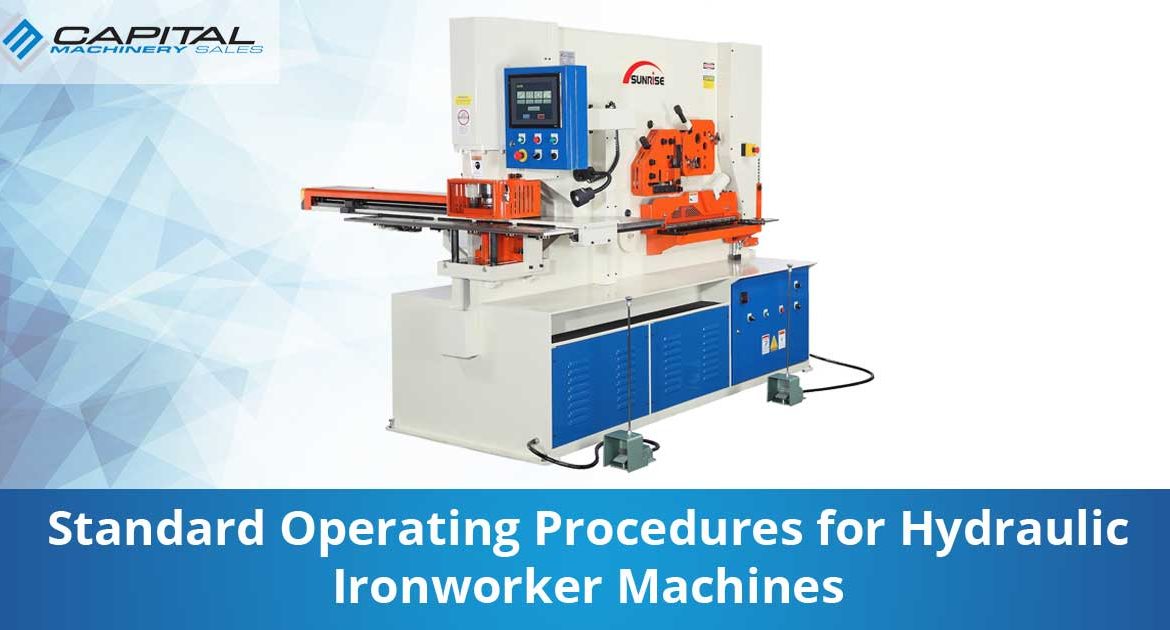
Standard Operating Procedures for Hydraulic Ironworker Machines
Safety
1. When handling the hydraulic ironworker machine, your foot should be completely out of the pedal box once you complete each cut on machines that are not equipped with some light curtains or other safe guards.
2. When shutting the machine down, observe proper shutdown procedures. Also observe the same shutdown procedures when changing punches, dies, shims and blades. You need to shut off the main power supply and have the key to switch in the off position especially when changing punches and dies.
3. Double checks to make sure all guards are tucked in place, as well as all table adjustment bolts are held tightly.
4. While the metal piece is being cut, never grab it. When removing small pieces from the blade, make sure to use a hook and not your fingers.
5. Never run the shear on ‘automatic’ unless of course you are properly trained by your designated area manager or expert.
6. Always remember to turn the power off when you leave the machine unattended.
7. Keep your hands off the hazardous area or the ‘pinch point’. If the piece is just way too large to let it sit on the ironworker table
without your assistance, then you only need to hold the part, but make sure that it is off the ironworker table and also make sure that no body part can get easily injured. This simply means, never get any of your body parts way too near the machine that can easily get injured.
Operation
1. Once you are done changing punches, blades, shims or dies, you need to lower the punch or shear by hand (or jog them) to make sure you check its clearance and alignment are ok. It is really highly recommended that the punch and die alignment is always checked before each setup and periodically especially on longer runs.
Before you install the punch or die into the ironworker machine, make sure they are slipped checked because if you overlook this part, it can cause the tool to get damaged or cause some injury.
2. Make sure that you always adjust the material hold-downs to let the material to just slide under before any attempt to shear. Never allow more than 1/8” clearance between the hold-down clam and the material. Always make sure you check to confirm that the blade is properly cleared. To do this, you must use the feeler gauges.
3. Remember to never put any material in through the back side of the shear. This is a dangerous thing to do. Always make the cut from the roller table side to make sure that material is held down properly.
4. It is highly recommended to never try to trim off a material that is way shorter than the material’s thickness.
5. Never cut any pieces of the material which has less than half an inch under the hold-down.
6. Always use the correct stripper insert or plate.
7. Punch depth needs to be correctly set to avoid the stripper from any damages.
8. You need to make sure that the stripper is fully engaged and tightened before any operations are done on it.
9. Never attempt to punch any material that is thicker than the punch’s diameter.
10. Make sure to put your tools back after every setup and practice good housekeeping all the time.