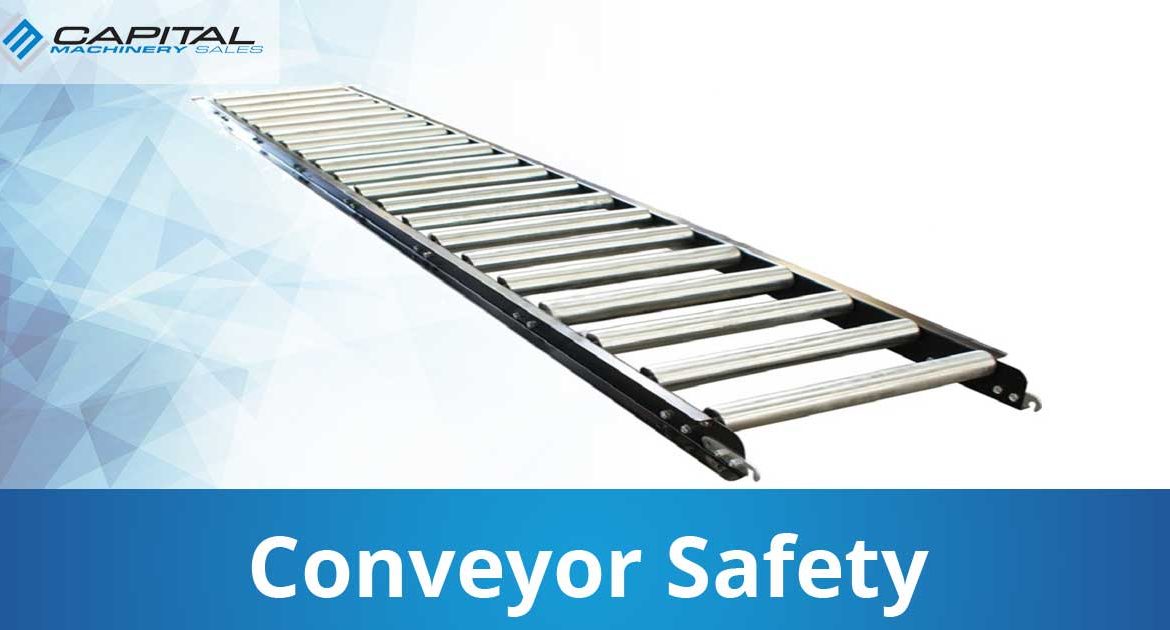
Conveyor Safety
Conveyors like any mechanical and electrical device have some safety concerns that need not be taken lightly. Because of the moving parts involved, anybody that works near or around these conveyors should be informed about conveyor safety. This is really very important.
Let us take a closer look on the Conveyor Equipment Manufacturers Association (CEMA) standards for package conveyors.
No climbing, standing, walking, riding or touching the conveyor at any given time.
If you fail to adhere or follow this rule, serious injury can occur. Just common sense, but knowing at times that people tend to get into mischief and not follow the rules, that there are injuries and equipment damages annually.
Never perform any maintenance when the electrical, hydraulic, air or gravity energy sources are on or unlocked.
Again, common sense is needed to follow this rule. For safety, only do maintenance on it if these energy sources are off or locked/blocked. You need to make sure to block the incline on a gravity conveyor belt before you work on it.
Even seasoned technicians can get into serious injuries are they get over confident in working around it or any given machinery and forget to unplug any electrical sources or other energy sources.
Make sure to have all approved covers and guards in place before you operate.
Conveyors have guards of covers for a reason, and that is safety! So if you operate without guards, it will be very unsafe and most common injuries and accidents occur because of this reason.
Guards can be detached by plant employees when they do maintenance or because it blocks someone’s access when working.
Avoid loading a stopped conveyor or overload a moving conveyor.
This help prevents your conveyors to get damaged right away or preserves it as it helps in avoiding overheating. It is important that conveyors are not overloaded when operating.
Make sure that all workers and personnel are clear of any equipment before operating.
It is important to practice before operating any conveyor that workers should be clear of any equipment. It is useful and considered better practice to install warning horns before any conveyor starts operating. Warning horns are inexpensive and very efficient.
Only allow authorised personnel in the area especially in operating or handling equipments.
Make sure only trained workers are around permitted to operate and do maintenance on the conveyors for two main reasons: safety and only trained personnel can maintain the conveyor to have it operate at its optimal performance.
No modification or misusing of conveyor controls.
Conveyor controls are any kind of electronic or any mechanical devices used when operating the conveyor. There is no need and should never be modified for any reason especially by personnel that is not qualified to do the job.
Make sure to keep any body parts, hair or clothing away from the conveyor especially when it is in operation.
This is the most common ways to get into an injury around the conveyor. So have the personnel keep their hands off the conveyor especially when it is in operation. Those having long hair, loose clothes or have longer ties need to be more careful around conveyors.
Remove any trash, papers and other unnecessary items or debris unless power is off or locked out.
It is crucial to have a clean environment around the conveyors and to any work place to avoid any accidents or injuries. As much as possible, make sure that the conveyor is working properly and efficiently. Never do the cleaning and maintenance work while the machine is still in operation. Familiarise yourself or whoever is the designated and trained personnel with conveyor safety.
Make sure all controls and pull-records are readily accessible or visible.
If in case there is a need for the conveyor to be stopped abruptly, you need to make sure the controls, levers or pull cords are accessible and are visible to anybody working in the area.
It is important to know the location and the function of all the start and stop controls of the conveyor.
For anybody who is working in the conveyor area, needs to be familiar with the location and function of all the start and stop controls. All controls should be marked to prevent any confusion and provide everyone with making quick decisions when using them.
Proper training is needed to be able to locate where they are, know when to use them and how to access them properly.
Make sure that any unsafe conditions are reported.
Any jamming needs to be cleared by authorised and trained personnel. Make sure that you practice satey not just around the conveyor area, but in your entire workshop to prevent any unnecessary injuries. Proper training and strict implementation of safety rules are very important. Any alert for potential safety concerns should be raised by the worker.